[深圳電路板廠]生產(chǎn)成本和產(chǎn)品質(zhì)量是所有生產(chǎn)商努力控制的兩個(gè)要素,但復(fù)雜的產(chǎn)品設(shè)計(jì)和諸多無(wú)法控制的隨機(jī)因素卻令這二者成了供應(yīng)鏈上的兩大瓶頸。解決成本與質(zhì)量之間矛盾的關(guān)鍵在于提高效率,只有通過有的放矢的測(cè)試和控制,才能翻越成本和質(zhì)量這兩座大山。本文以PCB檢測(cè)方案為例,用非常簡(jiǎn)單的事實(shí)和原則闡明了實(shí)現(xiàn)系統(tǒng)優(yōu)化的三個(gè)要素。而如何混合和調(diào)配這三個(gè)要素使之能夠適用于不同的生產(chǎn)和測(cè)試系統(tǒng),就是制造商實(shí)現(xiàn)“零缺陷”生產(chǎn)的基礎(chǔ)所在。
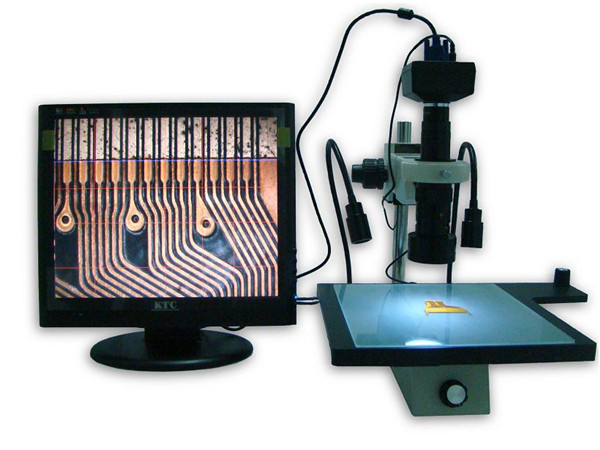
PCB制造業(yè)有一個(gè)夢(mèng)想,期望有朝一日能從“近乎完美”的原料和設(shè)計(jì)開始,經(jīng)由“近乎完美”的設(shè)備來(lái)加工,最后產(chǎn)出“近乎完美”的產(chǎn)品,而這當(dāng)中不必有任何既費(fèi)時(shí)又花錢的測(cè)試和檢驗(yàn)開銷。不幸的是,PCB產(chǎn)品復(fù)雜性的增加、瞬息萬(wàn)變的市場(chǎng)動(dòng)態(tài)以及來(lái)自企業(yè)內(nèi)部管理的挑戰(zhàn)、加上整個(gè)制造過程中諸多不確定的隨機(jī)因素,抵消了單純由原料、設(shè)計(jì)、設(shè)備和工藝進(jìn)步所帶來(lái)的好處。
今天,一般PCB的一次性成品率仍徘徊在60%到90%之間,如果不經(jīng)測(cè)試或返修,這無(wú)疑會(huì)造成巨大的浪費(fèi);而一旦有超過5%的次品流入市場(chǎng),其后果可能是災(zāi)難性的。看來(lái)生產(chǎn)“近乎完美”產(chǎn)品的夢(mèng)想終將落空,制造商仍必需繼續(xù)在檢測(cè)設(shè)備上大筆花錢,它們還不得不購(gòu)買新的設(shè)備,以便應(yīng)對(duì)新技術(shù)所帶來(lái)的新的測(cè)試挑戰(zhàn)。這一切似乎沒完沒了,掛在制造商脖子上的品質(zhì)獎(jiǎng)?wù)掠鷣?lái)愈沉重。
現(xiàn)在的問題是,能否合理地投資、配置和使用好昂貴的測(cè)試檢驗(yàn)設(shè)備,以使它們的效益盡可能發(fā)揮到極致。這樣,當(dāng)制造商大把大把從口袋里掏錢時(shí),能稍微心安理得一些。幸運(yùn)的是,的確存在讓制造商既花錢、又寬心的優(yōu)化檢測(cè)方案,它們的目標(biāo)是同時(shí)控制生產(chǎn)成本和產(chǎn)品質(zhì)量。這些方案經(jīng)過實(shí)踐檢驗(yàn),行之有效,而究其精髓,卻只是建立在少數(shù)簡(jiǎn)單的事實(shí)和原則之上:
1,控制缺陷傳播---產(chǎn)品缺陷越早發(fā)現(xiàn)則次品造成的經(jīng)濟(jì)損失越小。
2,降低冗余檢測(cè)---重復(fù)性缺陷檢測(cè)越少則檢測(cè)成本越低。
3,掌控質(zhì)量主敵---排序PCB缺陷比率,抑制頭號(hào)質(zhì)量殺手是事半功倍之舉。
這些簡(jiǎn)單的事實(shí)和原則構(gòu)成了優(yōu)化PCB檢測(cè)方案的三要素,對(duì)它們的綜合應(yīng)用可以幫助構(gòu)造不同的檢測(cè)方案,制造商應(yīng)該利用實(shí)際的生產(chǎn)數(shù)據(jù)對(duì)方案進(jìn)行定量分析,以評(píng)估方案的得失?,F(xiàn)在讓我們對(duì)以上三個(gè)方面作更詳盡的考察。
控制缺陷的傳播
如同水面上的擾動(dòng),其波及的范圍將隨著擾動(dòng)的傳播而擴(kuò)大,PCB制造中的缺陷,如不及時(shí)發(fā)現(xiàn),其造成的損失也會(huì)隨PCB從制造線的上游到下游逐漸擴(kuò)大。來(lái)自制造商的數(shù)據(jù)表明,對(duì)于中等復(fù)雜的PCB(譬如焊點(diǎn)在3,000左右,元件數(shù)在500左右),如果缺陷躲過當(dāng)前的檢測(cè),而在下一步檢測(cè)時(shí)才被發(fā)現(xiàn),則
電路板返修的平均費(fèi)用大約會(huì)增加6~7倍。同時(shí),
電路板報(bào)廢造成的損失也呈直線上升。
圖-2所示的簡(jiǎn)單模型向我們揭示了合理利用測(cè)試檢驗(yàn)設(shè)備,降低總體生產(chǎn)成本的一般思路。同時(shí),該模型也列出了在檢測(cè)效益分析中需要考慮的一些主要因素。首先,檢測(cè)設(shè)備應(yīng)按各個(gè)生產(chǎn)工序所引進(jìn)的缺陷類型合理配置,以便及時(shí)發(fā)現(xiàn)缺陷并為
電路板返修提供盡可能準(zhǔn)確的缺陷定位信息。其次,各檢測(cè)設(shè)備對(duì)相關(guān)缺陷的檢出率應(yīng)不低于某個(gè)下限,否則配置檢測(cè)設(shè)備將不會(huì)產(chǎn)生效益,可以根據(jù)工廠的利潤(rùn)目標(biāo)估算這個(gè)下限。最后,應(yīng)牢記在心的是,任何檢測(cè)設(shè)備都有可能在檢測(cè)過程中對(duì)
電路板本身造成損害(如人工目檢時(shí)的靜電、ICT測(cè)試時(shí)的背面驅(qū)動(dòng)電流等),檢測(cè)過程亦可能使整個(gè)生產(chǎn)線的節(jié)奏放慢。在更精細(xì)的檢測(cè)效益分析中,可以考慮這些負(fù)面因素。
降低冗余的檢測(cè)
在PCB的故障缺陷“頻譜”中,并非每一種檢測(cè)設(shè)備只覆蓋一個(gè)“窄帶”。簡(jiǎn)言之,一種檢測(cè)設(shè)備可能查出多種PCB的缺陷。圖1 是簡(jiǎn)化的故障覆蓋分配表,該表顯示,每一類型的缺陷有可能被多次重復(fù)檢查。例如,當(dāng)生產(chǎn)線上同時(shí)配有人工目檢(MVI)、自動(dòng)X-射線檢測(cè)(AXI)、和在線測(cè)試(ICT)時(shí),PCB的焊點(diǎn)開路缺陷將被重復(fù)檢查三次。對(duì)于軍用或醫(yī)用類的PCB來(lái)說(shuō),冗余的檢測(cè)可能是有用的,有時(shí)甚至必須這樣做,但對(duì)大多數(shù)民用類PCB來(lái)說(shuō),如此的冗余檢測(cè)可能是得不償失的。檢測(cè)設(shè)備供應(yīng)商和PCB制造商都已經(jīng)認(rèn)識(shí)到,它們可以在這里做一些文章來(lái)降低檢測(cè)成本,同時(shí)還可以維持住產(chǎn)品的質(zhì)量。所謂的“分布式”測(cè)試、檢驗(yàn)方案就是針對(duì)如何降低冗余檢測(cè)而言的。
分布式檢測(cè)方案,除了試圖減少冗余的測(cè)試外,還力求提高PCB總體的測(cè)試覆蓋率。做到這一點(diǎn)的關(guān)鍵在于對(duì)PCB缺陷分布規(guī)律有完全的了解、同時(shí)掌握各種測(cè)試技術(shù)的優(yōu)劣和PCB的CAD數(shù)據(jù),從而使合適的測(cè)試手段在合適的生產(chǎn)階段被用于檢測(cè)合適的的故障類型。目前在市場(chǎng)上已有商用的軟件用于自動(dòng)生成分布式檢測(cè)方案,如GenRad 公司的GR FORCE/Strategist。該軟件以PCB的CAD/BOM文件作為輸入,統(tǒng)籌包括自動(dòng)光學(xué)檢測(cè)儀(AOI)、自動(dòng)X-射線檢測(cè)儀(AXI)、飛針測(cè)試系統(tǒng)(FPT)、生產(chǎn)線缺陷分析儀(MDA)、在線測(cè)試系統(tǒng)(ICT)和功能測(cè)試系統(tǒng)(FCT)在內(nèi)的測(cè)試資源,輸出優(yōu)化的分布式檢測(cè)方案。
掌控質(zhì)量主敵
如同進(jìn)行作戰(zhàn),在和PCB 制造缺陷的較量中,必須了解清楚主要的對(duì)手。電子制造業(yè)有所謂的“80%-20%法則”,意思是說(shuō),百分之八十的質(zhì)量問題常常是因?yàn)?0%的制造缺陷引起的,而這20%正是產(chǎn)品質(zhì)量的主要?dú)⑹?。一個(gè)以效益和質(zhì)量并重的PCB檢測(cè)方案,應(yīng)該建立在對(duì)缺陷分布規(guī)律的完整認(rèn)識(shí)上,抓住主要的問題對(duì)癥下藥。
圖-4所示的PCB缺陷分布具有一般性,但并非每一種PCB和制造工藝都會(huì)產(chǎn)生相同的缺陷分布。制造商必需根據(jù)具體的PCB及其工藝對(duì)缺陷分布作出更精細(xì)的量化。
目前PCB制造總的缺陷分布趨勢(shì)是:制造引進(jìn)的結(jié)構(gòu)性缺陷(如焊點(diǎn)問題、貼裝偏差等)占七成左右,而元器件的電性能缺陷(如電參數(shù)偏差、IC功能失效等)占三成左右。正是這一缺陷分布趨勢(shì),改變了過去以電性能測(cè)試為主的檢測(cè)方案,并使得以光學(xué)(包括X-射線)檢測(cè)為代表的結(jié)構(gòu)性缺陷測(cè)試設(shè)備被廣泛應(yīng)用于生產(chǎn)中。
深入而言,由于封裝技術(shù)的進(jìn)步(μBGA、CSP等)和小型化的趨勢(shì),電性能測(cè)試對(duì)PCB組裝中引進(jìn)的近七成的結(jié)構(gòu)性缺陷已變得無(wú)能為力,因此檢測(cè)方案的著重點(diǎn)勢(shì)必以控制結(jié)構(gòu)性缺陷為主。
掌握缺陷控制的輕重緩急,對(duì)構(gòu)造合理的抽樣檢測(cè)方案亦至關(guān)重要。抽樣的頻度基本上正比于缺陷引起的失效頻度,由此產(chǎn)生的抽樣檢測(cè)開銷則趨于最低。
總結(jié)
我們已在此簡(jiǎn)述了優(yōu)化PCB檢測(cè)方案的三要素,如何去混合這些要素,調(diào)配出滿意的方案則需大量采集來(lái)自生產(chǎn)線的數(shù)據(jù)并靜下心來(lái)仔細(xì)劃算。它們可能幫你定性或定量回答諸如這樣的問題:能否購(gòu)置一臺(tái)貼封后的AOI設(shè)備,使得ICT測(cè)試的合格率提高5%?能否縮短10%的檢測(cè)時(shí)間,而次品率不至增加1%?但掌握了這些要素并不一定能準(zhǔn)確回答有關(guān)PCB檢測(cè)方案所有的問題。因?yàn)榧词贯槍?duì)“近乎完美”的制造過程,還會(huì)有不可避免亦不可救藥的隨機(jī)因素來(lái)模糊我們的估算,何況實(shí)際的制造過程可能充滿人為的誤差和影響產(chǎn)品質(zhì)量的額外要素。然而令人欣慰的是,前面提到的“80%-20%法則”在這里也成立,從而我們可以用較少的主要因素去幫助構(gòu)造PCB檢測(cè)方案,用來(lái)回答我們關(guān)心的大多數(shù)有關(guān)控制質(zhì)量和成本的問題。
關(guān)注[恒成和電路板]微信公眾平臺(tái),了解更多行業(yè)資訊和最新動(dòng)態(tài)!(微信號(hào):PCBHCH)
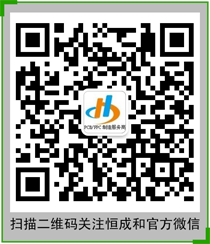